How does a VMC work?
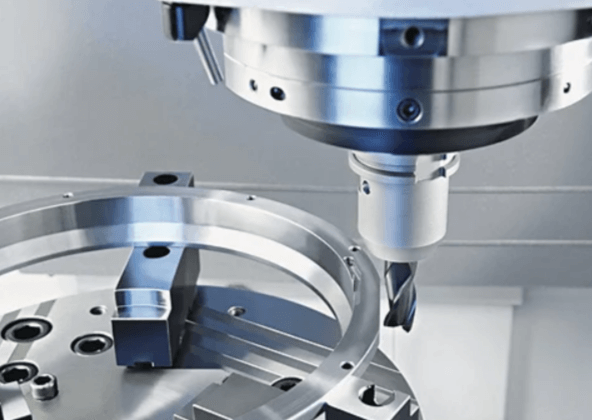
Introduction to VMC
Vertical Machining Centers (VMC) are sophisticated pieces of equipment used in the manufacturing industry to perform precise milling, drilling, and tapping operations. Their design features a vertical spindle that provides a unique advantage in terms of accuracy and efficiency.
Components of a VMC
A VMC is composed of several critical components, each playing a vital role in its operation:
- Structure and Frame: The foundation of the machine, providing stability and support.
- The Spindle: Heart of the VMC: This is where the tools are mounted and rotated to perform machining tasks.
- Tool Magazine and Tool Changer: These automate the process of switching tools during operations, enhancing efficiency.
- Control Panel: The Brain of VMC: Manages machine operations through user input and software control.
Types of VMCs
VMCs vary in type depending on their intended use and capabilities:
- Standard Vertical Machining Centers: Commonly used for a wide range of general manufacturing tasks.
- Advanced High-Speed VMCs: Designed for high precision and speed, suitable for complex manufacturing processes.
- Specialty VMCs for Unique Applications: Customized to meet specific industrial needs, such as those in aerospace or automotive sectors.
How Does a VMC Operate?
The Operational Workflow of a VMC
Operating a VMC involves several key steps:
- Setting Up the Machine: Preparing the VMC for operation, including tool setup and calibration.
- Tool Loading and Tool Change Process: Efficient changeovers are critical to minimizing downtime.
- The Machining Process: The core of VMC operations where the actual cutting, milling, or drilling takes place.
CNC Technology in VMCs
Computer Numerical Control (CNC) technology enhances the functionality and flexibility of VMCs:
- Role of CNC in Enhancing VMC Performance: Enables precise control over the machining processes.
- Programming CNC for Optimal Machining: Involves setting up the machine’s instructions to ensure optimal performance.
Automation and Robotics in VMCs
Incorporating automation and robotics can significantly boost a VMC’s productivity:
- Integration with Robotic Systems: Often used for material handling and parts loading/unloading.
- Benefits of Automation in VMC Operations: Increases production rates and consistency while reducing labor costs.
Applications and Benefits of Using a VMC
Diverse Applications of VMCs
VMCs are utilized in various sectors due to their versatility:
- VMCs in the Automotive Industry: Used for creating complex components like engine blocks and transmission cases.
- Aerospace Applications of VMCs: Ideal for producing the high-precision parts required in aerospace.
- Role in Consumer Electronics Manufacturing: Essential for fabricating small, intricate components.
Advantages of VMCs Over Other Machining Centers
VMCs offer several distinct advantages:
- Precision and Accuracy: Provide superior accuracy for detailed machining work.
- Speed and Efficiency: Capable of quickly producing parts with minimal waste.
- Customization and Flexibility: Easily adaptable to new production requirements.
Maintenance, Troubleshooting, and Safety in VMC Operations
Regular Maintenance of a VMC
Maintaining a VMC is essential for ensuring its longevity and performance:
- Routine Checks and Maintenance Schedule: Regular maintenance routines help prevent unexpected downtime.
- Longevity and Performance Optimization: Proper maintenance extends the life of the machine and maintains its performance.
Troubleshooting Common Issues in VMCs
Understanding common problems and how to fix them is crucial:
- Identifying and Resolving Operational Problems: Quick diagnosis and resolution of issues keep operations running smoothly.
- Tips from Industry Experts: Expert advice can help in efficiently managing and troubleshooting VMCs.
Safety Protocols for Operating a VMC
Safety is paramount when operating heavy machinery:
- Essential Safety Measures and Guidelines: Operators must follow strict safety protocols to ensure a safe working environment.
- Training and Safety Compliance in Workplaces: Ongoing training and adherence to safety standards are crucial for preventing accidents.
Future Trends and Innovations in VMC Technology
Technological Advances Impacting VMCs
The future of VMCs looks bright with continuous technological advancements:
- The Future of Automation in VMCs: Further integration of automation technologies to enhance efficiency.
- Sustainable Practices and Energy Efficiency: Increasing focus on reducing the environmental impact of manufacturing processes.
The Global Market and Future Outlook for VMCs
The VMC market is evolving rapidly:
- Market Trends and Growth Predictions: Expected growth due to increasing demand for precision machined components.
- Challenges and Opportunities in the VMC Industry: Adapting to new technologies and market conditions will be key to future success.
Conclusion
Recap of VMC Functionality and Impact
VMCs are essential tools in the manufacturing industry, known for their precision, efficiency, and adaptability.
The Future of Manufacturing with VMCs
As technology progresses, VMCs are expected to become even more versatile and integral to manufacturing processes, driving innovations and improvements across industries.
Frequently Asked Questions (FAQs)
- What makes a VMC different from a horizontal machining center? VMCs have a vertically oriented spindle which facilitates better chip evacuation and is generally more compact, making it suitable for smaller manufacturing spaces.
- How do CNC enhancements improve VMC operations? CNC technology provides precise control over machining processes, allowing for complex patterns and high-quality finishes.
- What are the initial setup requirements for a VMC? Initial setup includes installation, calibration, and programming to match specific manufacturing tasks.
- How can automation in VMCs reduce production times? Automation helps in faster tool changes and material handling, significantly cutting down production cycle times.
- What safety measures should be observed when operating a VMC? Safety measures include proper training, using protective equipment, and adhering to operational guidelines to prevent accidents.
- How frequently should maintenance be performed on a VMC? Maintenance schedules vary based on machine usage but typically include daily checks and more thorough inspections at regular intervals.