What is a Vertical Machining Center?
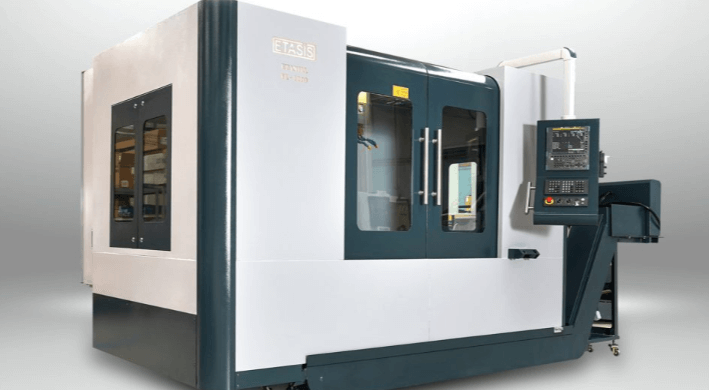
Introduction
Vertical Machining Centers (VMCs) are integral components in the toolkit of modern manufacturing facilities. Known for their precision and versatility, VMCs are utilized to perform a variety of machining tasks that are crucial for producing complex parts in a cost-effective manner. This guide offers a comprehensive look into the role of these machines in industrial applications.
What is a Vertical Machining Center?
A Vertical Machining Center is a sophisticated piece of equipment designed to handle various machining tasks with high precision. Positioned vertically, the spindle of a VMC allows the machine to execute operations like milling, drilling, and tapping directly on the surface of a workpiece. This section will explain the basic mechanics and components of a VMC.
Design and Features of Vertical Machining Centers
The design of Vertical Machining Centers is optimized for stability and precision. Key features include a powerful vertical spindle, advanced CNC control systems, and automatic tool changers which facilitate complex operations with minimal human intervention. Here, we’ll explore the technological innovations that enhance the functionality of these machines.
How Does a Vertical Machining Center Work?
Understanding the operational mechanics of a VMC is crucial for maximizing its capabilities. This section will cover the step-by-step process from setup to execution, detailing how the machine’s CNC system coordinates all movements to produce high-quality components.
Types of Vertical Machining Centers
There are several types of VMCs available, each tailored for specific manufacturing needs. From basic models ideal for small shops to advanced machines capable of handling complex and heavy parts, this part will discuss how to choose the right VMC for your applications.
Applications of Vertical Machining Centers
VMCs are utilized in a wide range of industries due to their ability to precisely cut various materials. Industries such as aerospace, automotive, and electronics rely on VMCs for producing intricate components essential for their products. This section highlights specific applications and the advantages they bring to these sectors.
Advantages of Using a Vertical Machining Center
The primary advantages of using a VMC include enhanced precision, reduced waste, and increased production efficiency. VMCs are particularly valuable in settings where detailed and accurate machining is required. This part will delve into these benefits and their implications for productivity and cost-effectiveness.
Challenges and Limitations
Despite their extensive capabilities, VMCs face certain limitations and challenges, such as size constraints and high operational costs. In this section, we will address these issues and discuss potential solutions to mitigate their impact on manufacturing processes.
Maintenance and Safety Guidelines
Regular maintenance and adherence to safety guidelines are essential for the longevity and safe operation of VMCs. This part provides practical tips on routine upkeep and outlines safety protocols to protect operators and ensure efficient machine performance.
Innovations in Vertical Machining Technology
The field of machining continuously evolves, with technological advancements significantly enhancing the capabilities of VMCs. Innovations in CNC technology, automation, and machine learning are some of the developments that will be covered in this section.
Choosing the Right Vertical Machining Center
Selecting an appropriate VMC for your manufacturing needs involves considering several factors, including machine capacity, flexibility, and technological compatibility. This section will guide you through the decision-making process, helping you find a machine that fits your specific requirements.
Case Studies
Real-world applications and success stories can provide valuable insights into the effectiveness of VMCs. This part will present case studies from various industries, illustrating how different companies have leveraged VMCs to enhance their manufacturing processes.
FAQs
- What materials can a Vertical Machining Center process?
- VMCs can efficiently process metals, plastics, and composites, making them highly versatile in manufacturing.
- How does a Vertical Machining Center differ from a Horizontal Machining Center?
- The main difference lies in the spindle orientation which influences the type of work each machine can handle most effectively.
- What is the typical cost of a Vertical Machining Center?
- Costs can vary widely, generally starting from $50,000 and can exceed several hundred thousand dollars depending on the machine’s capabilities and additional features.
- How are operators trained to use a Vertical Machining Center?
- Training usually encompasses both theoretical and hands-on instruction on machine operation, programming, and maintenance.
- What are signs that a Vertical Machining Center needs maintenance?
- Indicators include abnormal noises, decreased precision, and unexpected machine behaviors which suggest potential issues.
Conclusion
Vertical Machining Centers play a pivotal role in modern manufacturing, with their ability to streamline production processes and enhance product quality. Understanding their operation, capabilities, and maintenance can significantly impact the efficiency and profitability of manufacturing operations.